We Create Impossible Structures in Glass
First of all, why glass? Glass has excellent dielectric properties (low conductive losses), excellent thermal properties (thermally insulating) and is potentially very low cost. The biggest issue with glass is the difficulty of shaping it with small dimensions and high aspect ratios. Until recently, there were only a few ways to make tiny structures in glass, such as wet chemical or dry plasma etching, micromachining, and embossing. Due to its inert nature and amorphous structure, the only wet chemical etch available, hydrofluoric acid (HF), is isotropic. This results in a maximum aspect ratio (depth/width) of 0.5. Dry etching is another option and can produce higher aspect ratios, up to 8. Unfortunately, both wet and dry etching of glass are slow processes (< 1 µm hour). In the last decade or so, photo-imageable glass has been developed to the point where it can be used for 2.5D glass structures. In this method, glass is exposed to UV light through a mask and then baked to convert it to a ceramic phase, yielding a high etch selectivity in HF. This method can render aspect ratios of up to 60. However, for true 3D structures not much could be achieved – until now. Using ultra-short laser pulses from a femtosecond laser we can finally start to fabricate previously impossible structures in glass.
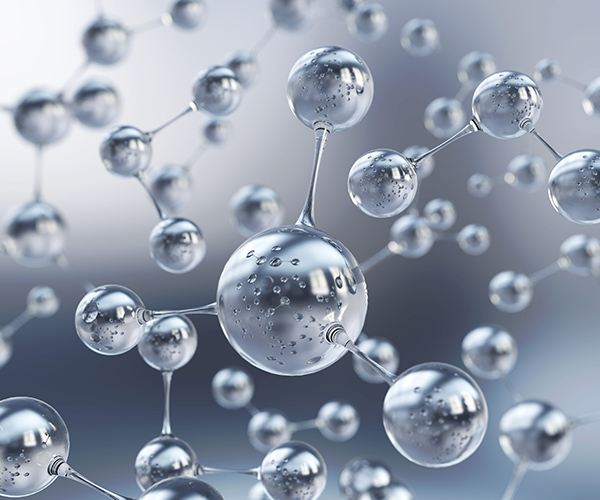
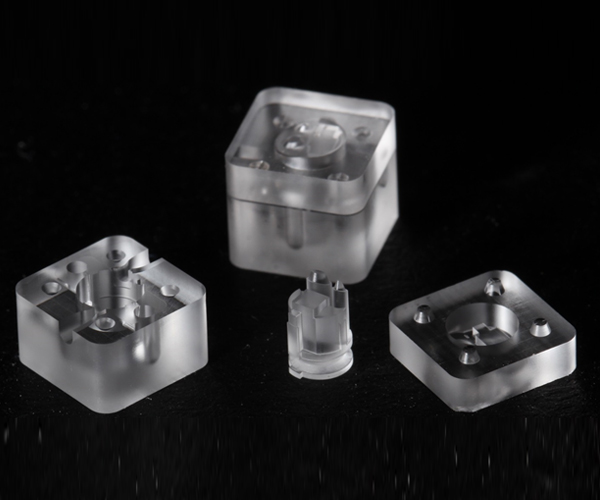
SLE process example: glass micromold
The Glass Structuring Process
To create our components we use a 3D glass structuring method called selective laser enhanced etching (SLE). SLE uses an ultra-short laser pulse, typically a few hundred picoseconds long, that is focused inside a transparent substrate, such as glass or fused silica for pattern transfer. With sufficiently high energy density the transparent material becomes opaque and quickly absorbs the pulse. Because of this, the absorption volume can be made very small – about a micron in diameter. Within this volume, the glass rapidly melts and refreezes, undergoing a change in morphology. When it is exposed to KOH wet chemistry, it etches much faster than the surrounding, untreated glass. The differential etch rate is generally between 1000 and 1500:1. The treated glass is removed and the untreated structure remains. SLE is unique in that, while it is a 3D printing technique, it is a subtractive rather than additive process.
Our components are fabricated on LightFab printers.
What can we print for you?